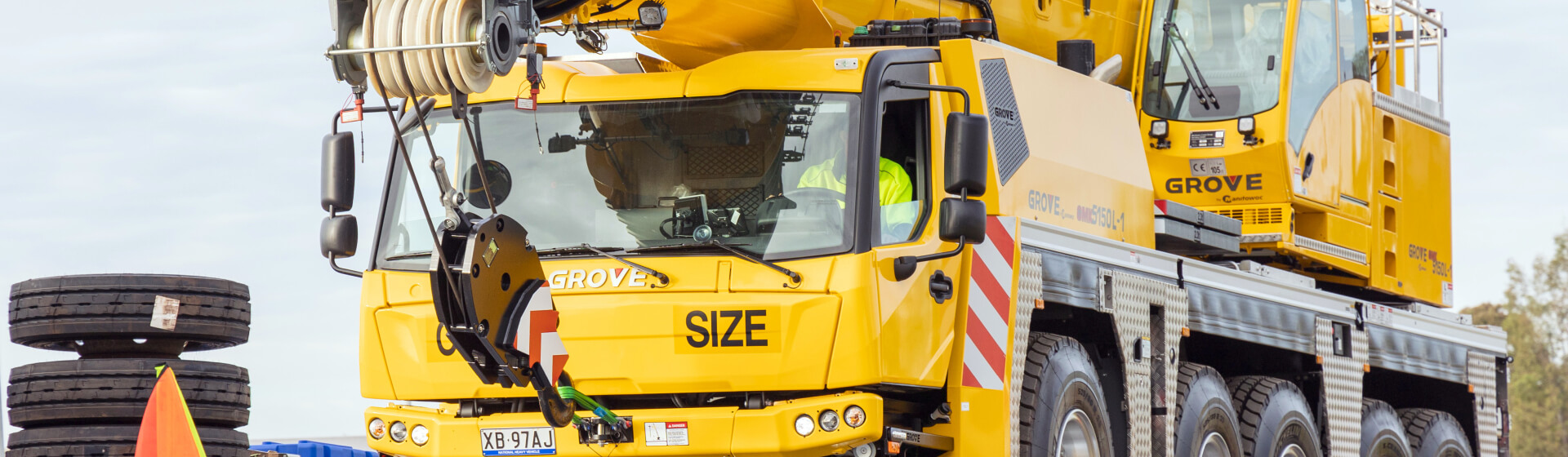
Two more Grove all-terrain cranes join large Tutt Bryant fleet for major Australian LNG plant turnaround
- New GMK6400 and GMK5250XL-1 arrivals joined an eight-strong Grove fleet to support an LNG plant shutdown close to Darwin, NT. Equipment supplier Tutt Bryant selected the cranes for their reliability and performance.
- The original fleet of eight cranes handled the first stage of the shutdown in 2021 and then new arrivals provided added lifting power for the second stage in 2022.
- A mix of four-, five- and six-axle cranes covered multiple tasks, with Manitowoc providing two on-site technicians to ensure maximum uptime.
A large and varied fleet of Grove all-terrain cranes worked on the second stage of a major turnaround project at one of the world’s largest, most complex LNG processing facilities – the INPEX-operated Ichthys LNG processing facility near Darwin in Australia’s Northern Territory. For the first stage of the turnaround, nationwide fleet hire and logistics solutions provider Tutt Bryant Heavy Lift & Shift sent a fleet of mobile cranes, mostly made up of Grove all-terrain cranes. Then for the second stage of the work, it sent an additional GMK6400 and GMK5250XL-1 to support operations.
As with the first stage, Manitowoc supplied 24/7 onsite technical support with two senior technicians who provided full-time coverage on a rotating basis. In addition to the new arrivals, the existing Grove fleet on the job was a mix of four-, five- and six-axle all-terrain models. A 90 t GMK4090 plus two 100 t GMK4100L-1 units; a 95 t GMK5095, 130 t GMK5130-2, and 150 t GMK5150L; plus two 300 t GMK6300L cranes.
“We carefully selected this fleet to provide a good mix of capacities for maximum flexibility, with their class-leading boom lengths providing optimized access to all areas of the plant,” said Rob West, senior divisional manager at Tutt Bryant. “We added the new models for extra capacity, fleet refreshment, and to provide more versatility. The long-boom GMK5250XL-1 means it can take on work where we previously relied on larger cranes. We purchased the GMK6400 because we knew we could use it for some heavier tasks, but we also knew we’d get good utilization from it in the future.”
Access all areas
Of particular value to the project was the Grove GMK5250XL-1, which launched in 2019. Offering the longest boom of any five-axle crane, its 78.5 m, eight-section MEGAFORM® boom can be further extended with an 8 m extension, or with an 11.2 m or 17.8 m swingaway jib plus 8 m jib extension. All these options mean an incredible 33.8 m of additional reach is possible. In conjunction with the MAXbase variable outrigger positioning system, which boosts capacities for increased jobsite flexibility, the crane can handle 9.9 t when the standard boom arrangement is at maximum height, or 1.3 t when at maximum working radius of 74m.
Even better, the crane’s impressive lifting power does not come at the expense of maneuvrability or compactness, with the GMK5250XL-1’s small footprint and all-wheel steer/crabbing modes delivering the highest levels of versatility.
“The lifts we undertook on the turnaround are all well within the capabilities of the cranes,” continued West. “But it was vital that work progressed smoothly as there were a lot of picks to perform so the plant could get back online as soon as possible. We’ve been really pleased with the reliability of the Grove cranes, as well as their speed, flexibility, and maneuverability.”
Hot stuff!
Putting added pressure on the cranes was the extreme heat and humidity of the local area plus a requirement for them to fit the 24/7 work schedule. But with their comfortable, air-conditioned cabs, the Grove cranes provided a pleasant work environment for the operators. And if any issues arose, one of the two Manitowoc technicians was on hand to offer support, keeping unexpected stoppages to a minimum. Delivering 24/7 coverage to ensure the Grove fleet remained at maximum operational strength reflects Manitowoc’s long-standing commitment to customer support.
“I can’t speak highly enough of the two Manitowoc technicians – during the first stage of the turnaround they worked seamlessly with our team and minimized any machine downtime,” said West. “On the project, there are no cell phones allowed. We expected this to cause some delays with service, but the Manitowoc guys have found solutions in minutes, rather than hours.”
CONTACT
Crystal Chi
Manitowoc
T +86 2164 570 066*103
crystal.chi@manitowoc.com