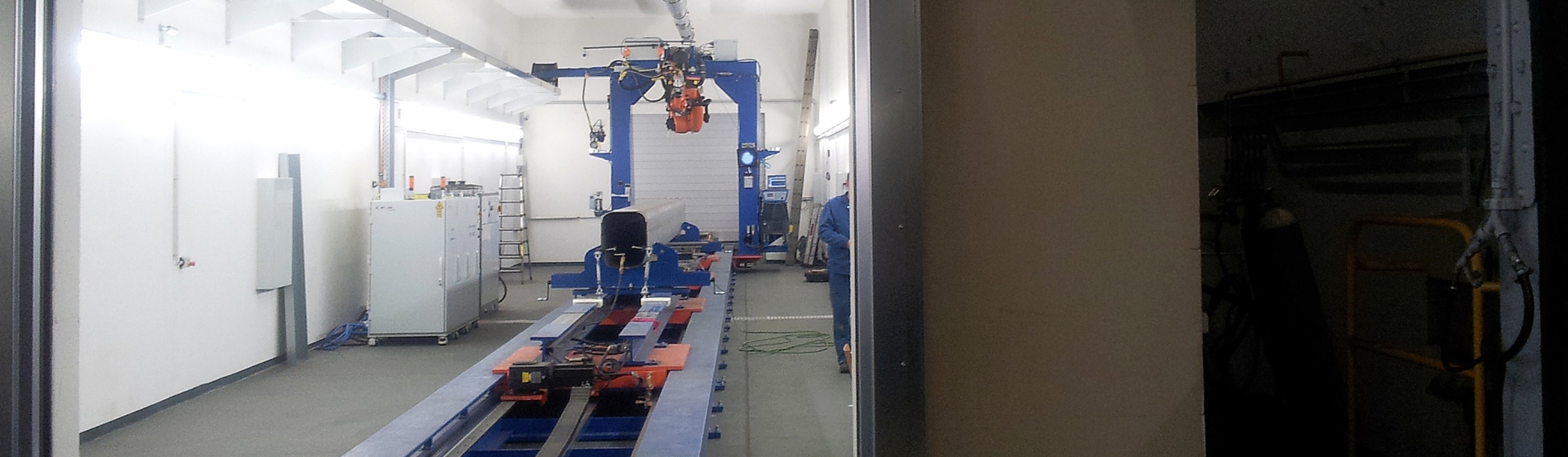
Manitowoc’s new laser welding technology adds value to Tecra’s Grove GMK5095
A significant investment in new welding technology at Manitowoc’s Wilhelmshaven facility in Germany is resulting in better booms for the company’s Grove GMK all-terrain cranes. The new laser-hybrid welding and cutting machine offers a level of precision that delivers noticeable improvements for customers using the cranes on the job site.
Michael Hüneke welding director for Manitowoc in EMEA said there were many advantages to the new system.
“To our knowledge this factory is the only one in the mobile crane industry to use this cutting-edge welding technology – and we are very proud of it ” he said. “The advantages are immediately obvious. For example we do much less manipulation of the steel prior to forming the boom which is better for maintaining and prolonging the structural integrity of the steel we use. It also uses less material than before and is much faster because we need to do less preparation before starting to weld.”
One of the latest companies to benefit from a GMK crane with a boom from the new laser welding set-up is Munich Germany-based crane rental company Tecra a subsidiary of Klema GmbH. The company took delivery of a new GMK5095 earlier this year and Wolfgang Klenner general manager of Klema GmbH explained the benefits his company sees from the crane and also the new welding process.
“In comparison with other crane models the Grove GMK5095 offers significantly higher capacity ” he says. “And since the boom is longer than most it gives us a clear competitive advantage. Here in Munich precise compliance with weight limits is crucial so when you’ve got a boom that’s been as highly engineered as this latest one on our GMK5095 you can see tangible benefits in terms of weight and design.”
The 100 t five-axle GMK5095 excels as a universally deployable taxi crane and it was one of the first Grove models to benefit from Manitowoc’s new laser-hybrid welding process at its Wilhelmshaven facility. Most competitors in the 95 t class are unable to match the Grove GMK5095’s combination of a 60 m main boom and 13.9 t of counterweight which can be carried on the crane while staying within German load limits.
Previously the Grove GMK5095’s boom shells were welded manually or semi-automatically. Today Manitowoc’s new laser-hybrid welding process joins the upper and lower shell of the boom by robot. While maintaining the same strength this process significantly reduces the need for filler material – by up to 120 kg on a 60 m boom.
With the laser-hybrid welding and cutting system there is no tacking of backing strip submerged arc welding or straightening required which improves the production rate for mobile crane booms. In addition the new machine requires lower heat input. All told this makes for greater efficiency better precision and less weight in Grove GMK boom constructions.
The new laser welding robot is housed in its own cab that stretches over a large part of the boom production line. In conjunction with its installation all workstations on the boom production line have been reorganized to better optimize work flow and ergonomics.
The end results are noticeable and the Grove GMK5095’s boom welding seams are barely visible after applying the topcoat says Sven Bauer technical manager of the Klema Group.
“The extremely high-finish quality of Grove cranes is emphasized with this new process ” he says. “Manitowoc assembles its cranes after applying the topcoat which gives them a lasting high-quality style distinguishing them from cranes that receive their topcoat post-assembly.”
Manitowoc modified its Grove all-terrain crane manufacturing process in Wilhelmshaven several years ago. Since then components receive their topcoat of paint before the crane is assembled. This has almost eliminated topcoat imperfections and reduces the risk of corrosion to zero.
The new welding system for booms replaces the previous submerged-arc welding unit.
Michael Hüneke says this latest investment at Wilhelmshaven was a continuation of a strong heritage of innovation in metal working at the facility.
“We see this as the latest in a long line of manufacturing innovations here at Wilhelmshaven ” he said. “We have over 80 years of manufacturing experience. Our history stretches from the origins of our steel work with riveting techniques through to the start of welding with non-coated electrodes and on to more modern gas or flux techniques before of course our latest innovation the laser system. All the while we have remained focused on providing our customers with the strongest lightest and most durable lifting equipment available.”
The Manitowoc factory in Wilhelmshaven produces all Grove GMK cranes of four axles or more from the 80 t capacity GMK4080-1 up to the 450 t capacity GMK7450.
Michael Hüneke welding director for Manitowoc in EMEA said there were many advantages to the new system.
“To our knowledge this factory is the only one in the mobile crane industry to use this cutting-edge welding technology – and we are very proud of it ” he said. “The advantages are immediately obvious. For example we do much less manipulation of the steel prior to forming the boom which is better for maintaining and prolonging the structural integrity of the steel we use. It also uses less material than before and is much faster because we need to do less preparation before starting to weld.”
One of the latest companies to benefit from a GMK crane with a boom from the new laser welding set-up is Munich Germany-based crane rental company Tecra a subsidiary of Klema GmbH. The company took delivery of a new GMK5095 earlier this year and Wolfgang Klenner general manager of Klema GmbH explained the benefits his company sees from the crane and also the new welding process.
“In comparison with other crane models the Grove GMK5095 offers significantly higher capacity ” he says. “And since the boom is longer than most it gives us a clear competitive advantage. Here in Munich precise compliance with weight limits is crucial so when you’ve got a boom that’s been as highly engineered as this latest one on our GMK5095 you can see tangible benefits in terms of weight and design.”
The 100 t five-axle GMK5095 excels as a universally deployable taxi crane and it was one of the first Grove models to benefit from Manitowoc’s new laser-hybrid welding process at its Wilhelmshaven facility. Most competitors in the 95 t class are unable to match the Grove GMK5095’s combination of a 60 m main boom and 13.9 t of counterweight which can be carried on the crane while staying within German load limits.
Previously the Grove GMK5095’s boom shells were welded manually or semi-automatically. Today Manitowoc’s new laser-hybrid welding process joins the upper and lower shell of the boom by robot. While maintaining the same strength this process significantly reduces the need for filler material – by up to 120 kg on a 60 m boom.
With the laser-hybrid welding and cutting system there is no tacking of backing strip submerged arc welding or straightening required which improves the production rate for mobile crane booms. In addition the new machine requires lower heat input. All told this makes for greater efficiency better precision and less weight in Grove GMK boom constructions.
The new laser welding robot is housed in its own cab that stretches over a large part of the boom production line. In conjunction with its installation all workstations on the boom production line have been reorganized to better optimize work flow and ergonomics.
The end results are noticeable and the Grove GMK5095’s boom welding seams are barely visible after applying the topcoat says Sven Bauer technical manager of the Klema Group.
“The extremely high-finish quality of Grove cranes is emphasized with this new process ” he says. “Manitowoc assembles its cranes after applying the topcoat which gives them a lasting high-quality style distinguishing them from cranes that receive their topcoat post-assembly.”
Manitowoc modified its Grove all-terrain crane manufacturing process in Wilhelmshaven several years ago. Since then components receive their topcoat of paint before the crane is assembled. This has almost eliminated topcoat imperfections and reduces the risk of corrosion to zero.
The new welding system for booms replaces the previous submerged-arc welding unit.
Michael Hüneke says this latest investment at Wilhelmshaven was a continuation of a strong heritage of innovation in metal working at the facility.
“We see this as the latest in a long line of manufacturing innovations here at Wilhelmshaven ” he said. “We have over 80 years of manufacturing experience. Our history stretches from the origins of our steel work with riveting techniques through to the start of welding with non-coated electrodes and on to more modern gas or flux techniques before of course our latest innovation the laser system. All the while we have remained focused on providing our customers with the strongest lightest and most durable lifting equipment available.”
The Manitowoc factory in Wilhelmshaven produces all Grove GMK cranes of four axles or more from the 80 t capacity GMK4080-1 up to the 450 t capacity GMK7450.