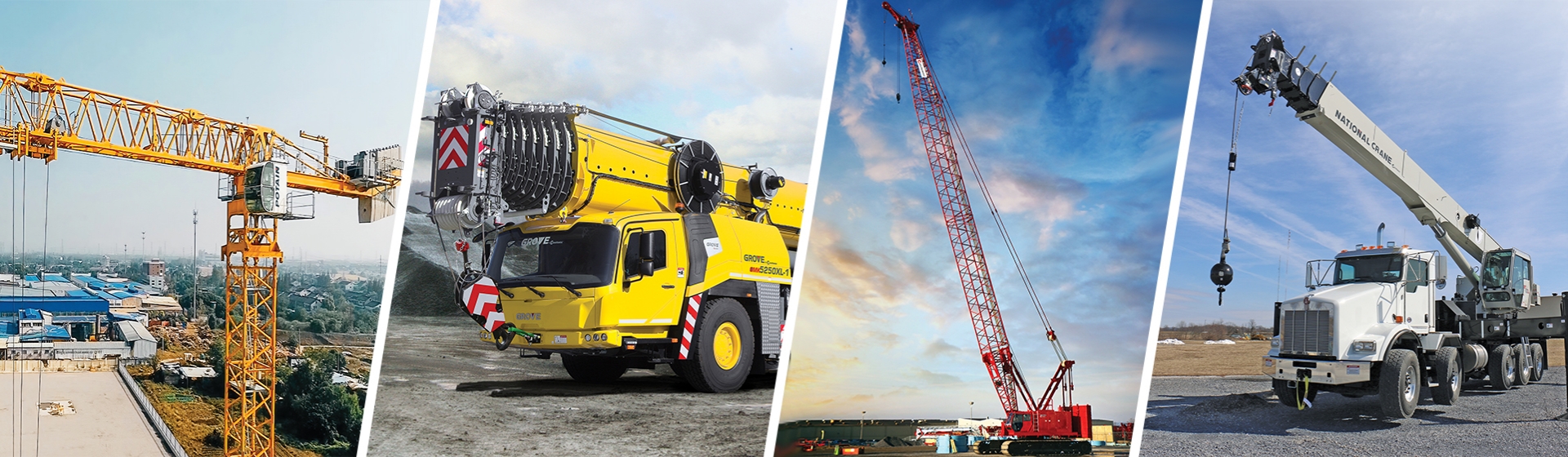
Manitowoc joins National Science Foundation-backed research project focused on job site safety through new technologies
Manitowoc Cranes will participate in a new project focused on safety of construction workers on job sites. The company will collaborate with the National Science Foundation (NSF) the Association of Equipment Manufacturers (AEM) High Industries Inc. the University of Illinois at Urbana-Champaign and Pennsylvania State University to create a new cyber-physical operation system (CPS) for construction equipment.
NSF has awarded a $650 000 grant to the project that will integrate advances in robotics computer vision and construction management. The goal is to create tools for the quick and easy planning of crane operations and incorporate them into a safe and efficient system that can monitor a crane’s environment and provide control feedback to the crane and operator. If successful the new system should have a positive effect on jobsite safety.
Lynn Dietrich director of engineering at Manitowoc said the project would tackle difficult and crucial challenges affecting crane operations.
“By applying state-of-the-art computing technologies the research will cover two of the most difficult challenges in crane operation and safety: stability and/or the structural overload of cranes and the potential for collision with other objects on job sites.”
Manitowoc will play an advisory role on the project as an industry expert for the collaborative project. It will also provide access to crane equipment job sites and technical capability information to the venture as well as the vetting of practical solutions borne from its research. Lancaster Pennsylvania-based High Industries will support the project as a crane user.
According to NSF the working hypothesis of the venture is that the monitoring and control of cranes can be performed using 3-D cameras robotics and computer vision algorithms to infer linear distances between objects and aid in collision detection. Also that detailed and continuous monitoring and control feedback can lead to improved planning and simulation of equipment operations.
The project will focus on developing methods for:
- Planning construction operations while accounting for hazards through simulation
- Developing analytics on the use of equipment
- Monitoring equipment surrounding the crane operating environment including hazard detection
- Proximity analysis to dynamic resources that include materials equipment and workers
- Providing crane stability feedback in real time
- Providing feedback to users in a “transparent cockpit” using visual and haptic cues
- Improving monitoring through model-driven and real-time 3D reconstruction techniques context driven object recognition and forecasting motion trajectories
“It’s not everyday a project like this comes along focused on the safety of workers and work site efficiency in our industry ” Dietrich said. “We’ve taken on this collaboration with a great sense of responsibility and conviction not only for Manitowoc but for the entire crane industry. By using advances in technology and computing we should be able to make significant steps in improving the efficient use of cranes on jobsites. We’re proud to be a partner in this noble effort.”
The collaborative project will begin January 1 2016 and is estimated to conclude December 31 2019.
NSF has awarded a $650 000 grant to the project that will integrate advances in robotics computer vision and construction management. The goal is to create tools for the quick and easy planning of crane operations and incorporate them into a safe and efficient system that can monitor a crane’s environment and provide control feedback to the crane and operator. If successful the new system should have a positive effect on jobsite safety.
Lynn Dietrich director of engineering at Manitowoc said the project would tackle difficult and crucial challenges affecting crane operations.
“By applying state-of-the-art computing technologies the research will cover two of the most difficult challenges in crane operation and safety: stability and/or the structural overload of cranes and the potential for collision with other objects on job sites.”
Manitowoc will play an advisory role on the project as an industry expert for the collaborative project. It will also provide access to crane equipment job sites and technical capability information to the venture as well as the vetting of practical solutions borne from its research. Lancaster Pennsylvania-based High Industries will support the project as a crane user.
According to NSF the working hypothesis of the venture is that the monitoring and control of cranes can be performed using 3-D cameras robotics and computer vision algorithms to infer linear distances between objects and aid in collision detection. Also that detailed and continuous monitoring and control feedback can lead to improved planning and simulation of equipment operations.
The project will focus on developing methods for:
- Planning construction operations while accounting for hazards through simulation
- Developing analytics on the use of equipment
- Monitoring equipment surrounding the crane operating environment including hazard detection
- Proximity analysis to dynamic resources that include materials equipment and workers
- Providing crane stability feedback in real time
- Providing feedback to users in a “transparent cockpit” using visual and haptic cues
- Improving monitoring through model-driven and real-time 3D reconstruction techniques context driven object recognition and forecasting motion trajectories
“It’s not everyday a project like this comes along focused on the safety of workers and work site efficiency in our industry ” Dietrich said. “We’ve taken on this collaboration with a great sense of responsibility and conviction not only for Manitowoc but for the entire crane industry. By using advances in technology and computing we should be able to make significant steps in improving the efficient use of cranes on jobsites. We’re proud to be a partner in this noble effort.”
The collaborative project will begin January 1 2016 and is estimated to conclude December 31 2019.