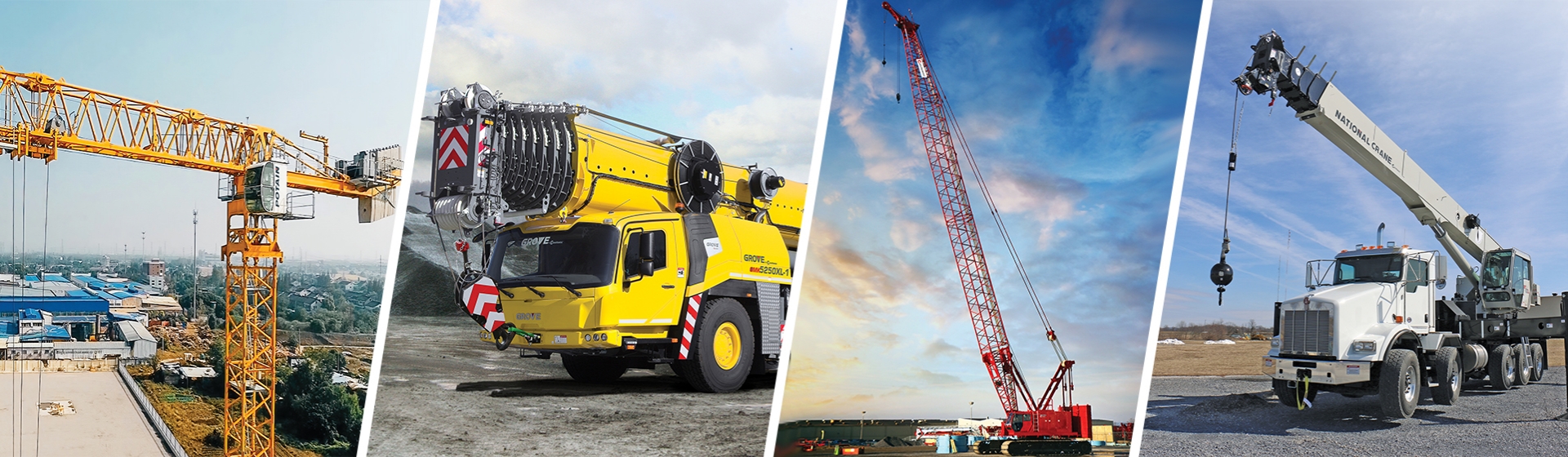
Manhattan Road & Bridge uses Grove GHC75 to increase efficiency on highway projects
- Manhattan Road & Bridge has discovered the benefits of using a Grove GHC75 telescoping crawler crane on drilled shaft installation projects in the state of Oklahoma.
- Since the GHC75 is easy to transport and does not need to be set up on outriggers the crane offered Manhattan the mobility and efficiency to stay on schedule.
- Manhattan’s operators found the GHC75’s controls and Rate Capacity Limiter to be intuitive and user-friendly and the crane’s cabin provided maximum vision and comfort on the job site.
Companies across North America are seeing the benefits of using a Grove telescoping crawler crane. For a variety of job sites the combination of crawler maneuverability telescoping boom versatility and 100 percent pick-and-carry function that they offer can increase efficiency and ROI.
Tulsa Oklahoma-based Manhattan Road & Bridge (Manhattan) is one such company. It works on highway projects across its home state many of which involve repetitive lifts along lengthy stretches of roadway. On the advice of its dealer the company began using a Grove GHC75 for many of its projects and is seeing an uptick in efficiency.
Manhattan’s use of the GHC75 began after the company was contracted by the Oklahoma Department of Transportation (ODOT) to install a series of drilled shafts along a stretch of Interstate Highway 35 that runs through the city of Norman. The work called for a maneuverable user-friendly crane to get the job done quickly so Manhattan turned to its dealer Kirby-Smith Machinery for a solution.
Kirby-Smith recommended the 75 USt GHC75 for the project for its easy transport both to the job and onsite. Because the crane would be moving up and down the highway to install the series of drilled shafts a model that didn’t need to be set up for each lift would guarantee efficiency. Also easy transport to the job site would mean an increase in ROI for the company.
Landry Logan project manager for Manhattan explained how the company used the crane.
“After digging a pilot hole we used the GHC75 with a hammer attached to drive the casing into the hole ” he explained. “When that was done we finished drilling and used the crane to set steel. Then we poured concrete to a certain height and pulled the casing out.”
Each shaft measured nearly 36 ft in depth with a diameter of 54 in. The hammer and casings together weighed about 17.5 USt. Manhattan was so impressed with the GHC75 that it employed the crane on additional job sites.
“We used the crane on a similar project in Oklahoma City ” recalled Logan. “The drill shafts there were 36 ft to 58 ft in depth at a diameter of 60 in. The GHC75 easily handled the workload but the biggest advantages were mobility and quick set up. We didn’t have to break down the crane to transport it. We just loaded it up on a trailer and moved to the next stop.”
The GHC75 can be easily moved in only one or two loads. The upper counterweight is removed or installed hydraulically and the carbody counterweight installs easily via a self-assembly system. The crane’s compact design provides greater versatility to work on a wide variety of projects and jobsites.
With its main boom and extension the GHC75 has a maximum tip height of 151 feet which provided easy access for operators during the lifts. The crane’s four-section main boom can telescope under load from 36 ft to 118 ft allowing for added flexibility. In addition an offsettable swingaway boom extension that measures 26 ft 3 in has offsets at 0 20 and 40 degrees.
Quality controls
The ergonomic design of the operator’s cab delivers maximum comfort while incorporating conveniently located joystick controls for precise operation. The cab tilts up to 20 degrees and comes equipped with an air-suspension seat color monitor for up to four cameras and precise climate control.
In both Norman and Oklahoma City the GHC75’s intuitive controls and comfortable cab received ample praise from Manhattan’s crew.
“The joystick controls make it easy to run ” said Chris Mitchell operator for Manhattan. “It’s comfortable with plenty of leg room and good visibility to see the pick. The crane has excellent maneuverability and mobility. Overall I’m impressed.”
Jesus Nunez operator for Manhattan lauded the crane’s Rated Capacity Limiter with graphical display which provides operating parameters and advanced real-time diagnostics.
“Everything was well within the crane’s capabilities ” he explained. “The machine tells you how much boom you have out and how much you can pick enabling us to lift more efficiently. I really liked running it and the comfort was very good.”
Kirby-Smith Machinery has been a leading distributor of heavy equipment and cranes in the central U.S. for more than 30 years. The Oklahoma City-based company serves a wide array of industries from its 10 full-service locations including construction paving industrial aggregate pipeline services and many others.
Manhattan Road & Bridge tackles a wide variety of bridge and heavy infrastructure construction projects from its locations in Tulsa and Oklahoma City Oklahoma; Little Rock and Springdale Arkansas; and Fort Myers Florida. The firm offers many services including turnkey road and bridge projects bridge-repair services and pile-driving capacities of any design.